Zero Defects, n.: The result of shutting down a production line.
In a world where efficiency and productivity are at an all-time high, the term "zero defects" has gained traction as a new industry standard for quality assurance and manufacturing excellence
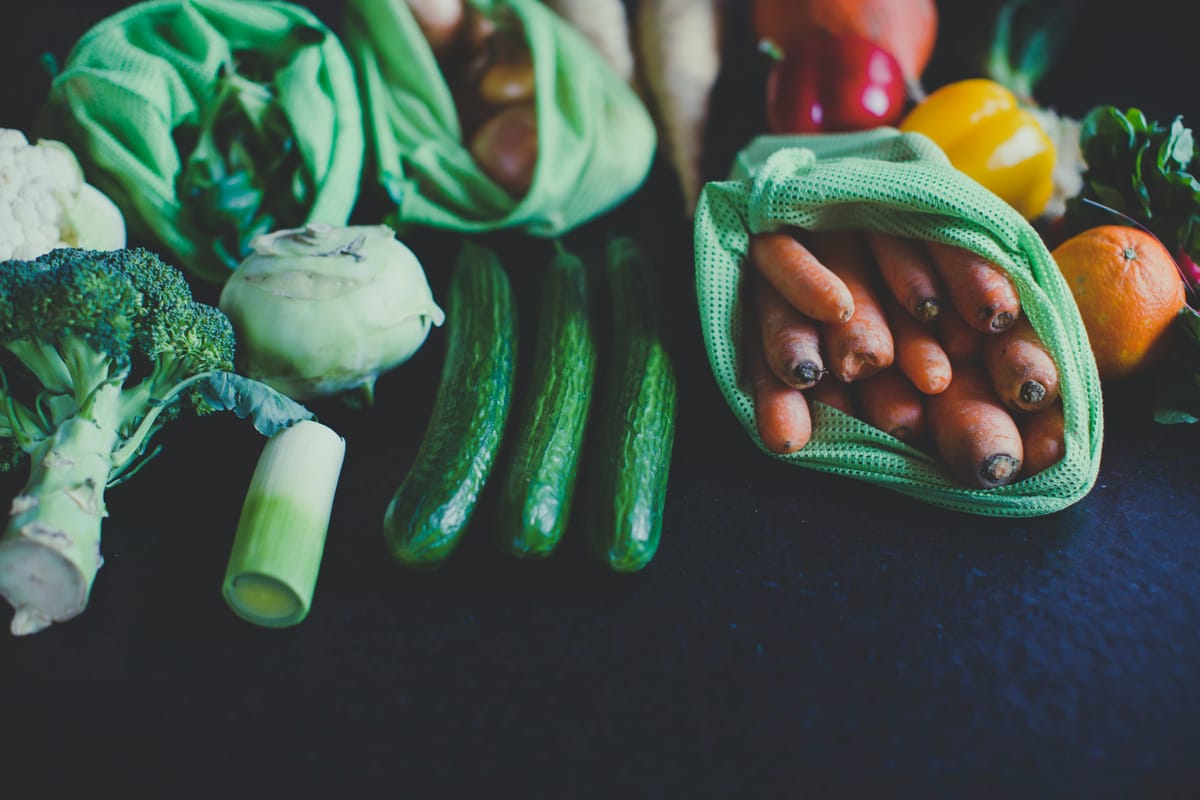
In a world where efficiency and productivity are at an all-time high, the term "zero defects" has gained traction as a new industry standard for quality assurance and manufacturing excellence. Originating from a Japanese philosophy known as Kaizen, the concept of zero defects aims to identify and eliminate errors and flaws in the production process, thus ensuring that each product meets or even surpasses the expected quality standards.
This revolutionary approach to manufacturing has not only captured the attention of business leaders across industries but also inspired a new generation of entrepreneurs to rethink the traditional ways of running their operations. Companies from various sectors, including automotive, electronics, and healthcare, have embraced this strategy in their quest for perfection. The pursuit of zero defects has led to numerous advancements in technology, processes, and human resources, as organizations strive to maintain a competitive edge in the global marketplace.
One key element that drives the success of companies adopting the "zero defects" philosophy is the continuous improvement methodology embedded within their culture. Employees at all levels of the organizational hierarchy are encouraged to actively participate in identifying potential errors and inefficiencies, as well as proposing innovative solutions for rectifying these issues. This collaborative spirit fosters a sense of ownership among team members and ultimately leads to better-informed decision-making and improved product quality.
To further accelerate the rate at which organizations can achieve their zero defects goals, various tools have been developed to assist in the process. For instance, computerized systems such as Enterprise Resource Planning (ERP) software provide real-time insights into production line performance, allowing managers to swiftly address any discrepancies that may arise. Similarly, advanced sensors and machine learning algorithms can be integrated into manufacturing equipment, enabling it to detect and correct potential flaws in the process before they become costly defects.
The implementation of zero defects strategies has also led to significant benefits for both employees and consumers alike. By investing in employee training and development programs, companies not only equip their workforces with the skills needed to excel in their respective fields but also create a conducive environment for fostering innovation and creativity. As a result, workers are more likely to remain loyal to their organizations, contributing to lower turnover rates and reduced recruitment costs.
On the other hand, customers reap the rewards of improved product quality when purchasing goods and services from companies committed to achieving zero defects standards. In addition to enjoying enhanced reliability and durability in their purchases, they also benefit from reduced repair and replacement costs, which ultimately translates into long-term savings.
However, it is essential to note that striving for zero defects does not imply perfection but rather an ongoing quest for improvement. The concept itself acknowledges that no production line can ever be entirely free of errors, as even the most meticulously designed systems are susceptible to unforeseen disruptions or human oversight. As such, companies pursuing this philosophy must remain adaptable and open-minded in their approach to addressing potential shortcomings.
Furthermore, the adoption of zero defects methodologies necessitates a significant shift in mindset for many organizations accustomed to more traditional management styles. In order to successfully implement these strategies, companies must be willing to invest time and resources into training employees on new methodologies and fostering a culture of continuous improvement.
In conclusion, the concept of zero defects represents a paradigm shift in modern manufacturing practices, with far-reaching implications for both businesses and consumers alike. By embracing this philosophy and its associated tools and methodologies, organizations can foster a culture of innovation and excellence, ultimately leading to improved product quality and consumer satisfaction. As we continue to navigate an ever-evolving global landscape, the pursuit of zero defects will undoubtedly play a pivotal role in shaping the future of industry standards.